Collaborative robots, or cobots, are changing the game in warehouse operations. These aren’t your typical robots; they’re designed to work with humans, not replace them. By handling daily and physically demanding tasks, cobots free up human workers to focus on more complex and rewarding activities. This synergy boosts productivity and makes the workplace safer and more efficient. As warehouses strive to meet the demands of modern logistics, cobots are emerging as vital tools in streamlining processes and enhancing overall performance.
Key Takeaways
- Collaborative robots reduce unnecessary walking, saving time and boosting performance.
- They help in minimizing human errors, ensuring accuracy in order fulfillment.
- Cobots enhance safety by handling tasks that could lead to injury if performed by humans.
- These robots offer flexibility, adapting quickly to changing warehouse needs.
- By working under humans, cobots improve job satisfaction and reduce fatigue.
Enhancing Efficiency Through Collaborative Robot Automation
Streamlining Repetitive Tasks
Repetitive tasks can be a drain on time and energy. Enter Cobot efficiency in warehouses significantly enhances productivity by streamlining operations. These collaborative robots, tackle mundane tasks like sorting and transporting items. This frees up human workers to focus on more complex duties. By handling repetitive tasks, they reduce fatigue and boost overall work quality. Plus, with the benefits of collaborative robots, tasks can be completed faster and more accurately. flexible automation systems, warehouses can easily adjust to changes in demand without a hitch.
Reducing Human Error
Mistakes happen, especially when humans are tired or overworked. Robotics help cut down these errors by consistently performing tasks with precision, which enhances quality control. They don’t get tired or distracted, which means fewer mistakes and contributes to quality control. This is where intelligent material handling comes into play. By automating the handling process, cobots ensure that items are sorted and stored accurately, reducing costly errors.
Optimizing Workflow Processes
Cobots aren’t just about doing tasks; they’re about doing them smarter. With advanced picking technologies, they can also optimize the way items are picked and packed. They analyze data to find the most efficient paths and methods, speeding up the entire process. This not only saves time but also improves the workflow, making operations smoother and more efficient, ultimately benefiting the supply chain. By integrating these technologies, a workplace can achieve a new level of efficiency.
Improving Safety Standards
Minimizing Workplace Accidents
In warehouses, safety is a top priority. Collaborative robots, or cobots, are designed to enhance safety by taking over repetitive and dangerous tasks, allowing human workers to focus on safer activities. These robots are equipped with sensors and artificial intelligence technologies that help them detect obstacles and people, reducing the risk of accidents. By automating tasks like lifting heavy items or moving goods across the work area, a robot can minimize the physical strain on workers and decrease the likelihood of injury. Additionally, with advanced collaborative robots performing these tasks, the workspace becomes less congested, further reducing the chance of accidents.
Implementing Safety Protocols
Safety protocols are crucial for maintaining a secure working environment. Robots play a significant role in this by adhering to strict safety guidelines. They are programmed to stop automatically if they sense any unexpected human interaction, ensuring that workers are not put in harm’s way. Training programs are essential for workers to understand how to work alongside these robots safely. Employees need to be aware of emergency procedures and how to interact effectively. Regular safety audits and updates to protocols ensure that both human and robot interactions remain safe and efficient. This continuous monitoring and adaptation help maintain a balance between safety and productivity.
Facilitating Seamless Human-Robot Collaboration
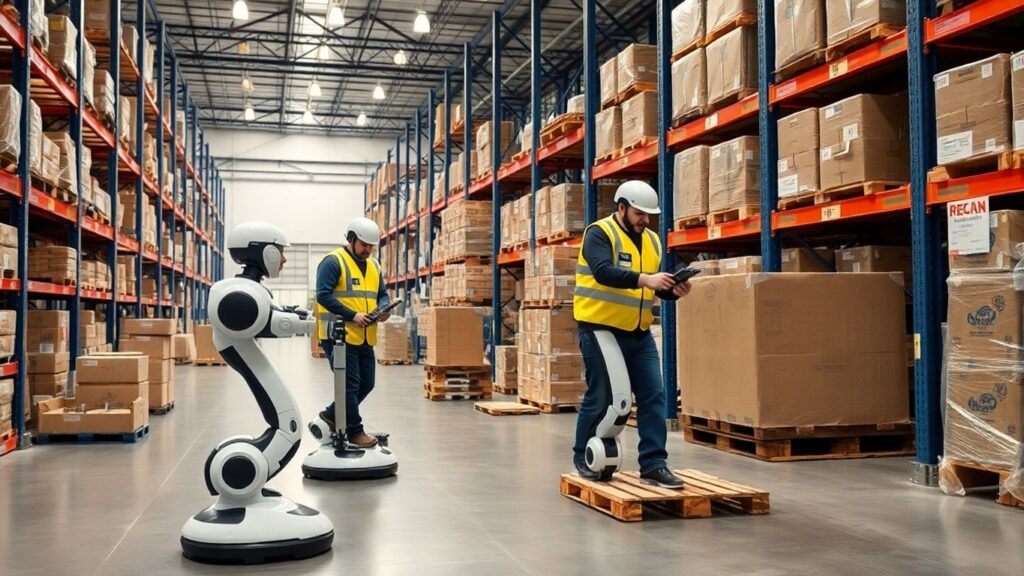
In modern warehouses, the fusion of human skills with robotic efficiency is transforming productivity. Human-robot collaboration is all about optimizing tasks where both entities bring their strengths to the table.
Cooperative Task Management
Warehouse automation with co-bots allows for a division of labor that plays to the strengths of both humans and robots. Workers handle tasks that require judgment and adaptability, while robots take on repetitive, precision-oriented jobs. This synergy results in:
- Enhanced efficiency: Robots perform tasks like sorting and transporting goods, freeing up human workers for more complex duties.
- Reduced physical strain: By taking over heavy lifting, help minimize worker fatigue and injury.
- Improved task allocation: Collaborative robot task optimization ensures that both humans and robots focus on what they do best.
Real-Time Communication
For effective collaboration, real time communication between humans and robots is crucial. AI-powered collaborative robots use sensors and advanced algorithms to understand and react to their surroundings. This capability allows for:
- Dynamic task adjustments Robots can adapt to changes in the workflow through machine learning, ensuring smooth operations and increasing overall efficiency.
- Immediate feedback: Workers receive instant updates on task progress, aiding in quick decision-making.
- Increased safety: Real time data processing helps prevent accidents, enhancing overall worker-robot team performance.
Shared Workspaces
In shared workspaces, humans and robots work side by side, each complementing the other’s abilities, which enhances output. This setup is made possible by technologies like ROBOTCORE Collaborative, which ensures safe and efficient interactions. Key benefits include:
- Efficient space utilization: Co-bots navigate shared areas without disrupting human activities.
- Enhanced collaboration: Workers and robots coordinate on tasks like order picking, and boosting Robot-assisted order fulfillment.
- Scalable operations: As demand fluctuates, the integration of robots allows for quick scaling of operations without the need for extensive retraining.
Boosting Flexibility in Operations
Adapting to Changing Demands
In the fast-paced world of warehousing, Flexibility is key to enhancing productivity within automated systems.. Collaborative robots, or cobots, are game-changers when it comes to adapting to fluctuating demands. Unlike traditional automation systems that are rigid and fixed, they can be easily reprogrammed to tackle different tasks as needed. This means that during peak seasons or unexpected surges, warehouses can adjust without missing a beat. Businesses can choose to either purchase enough robotics for normal operations and rent additional ones during busy periods or even shift between facilities to balance workloads. This adaptability not only keeps operations smooth but also helps in maintaining warehouse automation efficiency.
Supporting Diverse Tasks
Robotics are like the Swiss Army knives of the warehouse. They can handle a variety of tasks, from picking and packing to sorting and transporting goods. This versatility means that workers can focus on more complex duties while cobots take care of the repetitive and mundane. With their ability to perform multiple roles, making it easier to allocate resources where they’re needed most, ensuring that every part of the warehouse is running at full throttle.
Scaling Operations Quickly
One of the standout features of co-bots is how quickly they can be deployed. Unlike traditional systems that require months of installation and testing, they can be up and running in just a few weeks. This rapid deployment is crucial for businesses looking to scale operations quickly in response to market demands. Whether a company is expanding its footprint or just needs to ramp up production temporarily, moreover, they provide a scalable solution that doesn’t require a huge upfront investment. Plus, their mobility allows them to be transferred between sites with ease, making them an ideal choice for multi-location operations.
Reducing Operational Costs
Lowering Labor Costs
Incorporating collaborative robots into warehouse operations significantly reduces labor costs. These robots, often referred to as cobots, work side-by-side with human employees, tackling repetitive tasks and allowing workers to focus on more complex duties. This synergy helps warehouses avoid the need to hire additional staff, especially during peak seasons. With smart warehouse operations, the efficiency of both human and robotic workforce is maximized, leading to substantial savings.
Decreasing Downtime
Cobots help in minimizing downtime by maintaining a consistent workflow. Unlike humans, robots don’t require breaks and can operate around the clock. They are less prone to errors and can quickly adapt to changes in the workflow, ensuring that operations continue smoothly. This continuous operation is enhanced by real time inventory management systems, which keep track of stock levels and prevent disruptions caused by inventory shortages.
Enhancing Resource Utilization
With cobots, warehouses can optimize their resource utilization. These robots are equipped with advanced sensors and AI, allowing them to efficiently manage tasks such as sorting, picking, and packing. This not only speeds up these processes but also reduces the wear and tear on equipment and facilities. By integrating robotics into the workflow, warehouses can better allocate their resources, leading to improved operational efficiency and cost savings.
Increasing Job Satisfaction Among Workers
Fostering Skill Development
Collaborative robotics are reshaping how tasks are approached in the warehouse. By taking over monotonous and physically taxing duties, they allow workers to focus on more engaging roles that require decision-making and creativity. This shift not only alleviates physical strain but also encourages workers to develop new skills and advance their careers. Warehouse workforce augmentation through co-bots means employees can learn to operate and interact with advanced technology, broadening their skill set and increasing their value in the job market.
Encouraging Team Dynamics
Co-bots are not just tools but team players. They work alongside humans, creating a collaborative environment where team dynamics can truly flourish. This partnership fosters a sense of camaraderie and shared purpose among workers, as everyone contributes to the warehouse’s success. Employees often find that working with robotics reduces stress and enhances their ability to manage workloads effectively, leading to a more harmonious workplace atmosphere.
Improving Job Satisfaction
By reducing the physical demands of warehouse work, co-bots help create a more sustainable work environment. Employees can maintain a steady pace without the exhaustion that comes from repetitive manual tasks. This improvement in working conditions directly impacts job satisfaction, as workers feel more valued and less like cogs in a machine. As a result, turnover rates can decrease, and overall morale within the warehouse can rise, making it a more attractive place to work.
Leveraging Data for Continuous Improvement
Analyzing Performance Metrics
In the bustling world of warehouse operations, data is king. Collaborative robots, or cobots, are not just about doing tasks; they’re about doing them better each time. By collecting detailed performance metrics, these robots help warehouse managers see what’s working and what’s not. This data-driven approach can pinpoint inefficiencies and highlight areas that need a tweak. Imagine having a dashboard that shows you exactly how many items were picked, packed, and shipped in real time. It’s like having a pulse on your warehouse operations, allowing you to make informed decisions on the fly.
Identifying Bottlenecks
No one likes a traffic jam, especially in a warehouse. Cobots help in spotting bottlenecks that slow down operations. With continuous data collection, you can see exactly where things are getting stuck. Is it the packing station? Or maybe the loading dock? By identifying these choke points, you can reallocate resources or redesign workflows to keep things moving smoothly. Think of it as having a GPS for your warehouse that helps you avoid the rush hour.
Read about: Rodin AI Text to 3D: How to Turn Your Ideas into 3D Models
Implementing Feedback Loops
Feedback is crucial for improvement, and cobots are all about it. By using data, they create feedback loops that inform workers and managers about what’s going well and what needs adjustment. This isn’t just about fixing problems; it’s about creating a culture of continuous improvement. Regular updates and reports can guide training sessions, helping workers adapt and improve their skills. It’s like having a personal coach in the warehouse, always ready to help you do better.
Frequently Asked Questions
What are collaborative robots?
Collaborative robots are machines designed to work with humans to perform tasks like picking, packing, and moving items in warehouses, providing the benefits of collaborative work. They help make work easier and safer for people.
How do collaborative robots improve productivity?
Collaborative robots speed up work by helping with repetitive tasks and guiding workers through their jobs. This reduces the time spent walking and allows workers to focus on more important tasks.
Are collaborative robots safe to use in warehouses?
Yes, collaborative robots are designed with sensors to avoid collisions with people and objects. They help make the workplace safer by reducing accidents and injuries, which ultimately increases productivity.
Can collaborative robots replace human workers?
No, collaborative robots are meant to work with humans, not replace them. They assist with tasks that are hard or boring, letting people do jobs that require thinking and decision-making.
How flexible are collaborative robots in warehouse operations?
Collaborative robots are very flexible. They can be programmed to handle different tasks and can be rented or bought to meet changing demands in warehouses.
Do collaborative robots reduce operational costs?
Yes, they help lower costs by making workers more efficient, reducing errors, and decreasing the need for extra labor, especially during busy times.